An organization structure can be defined as the framework of a company that describes the entire structure and functioning of the company. Organization structures are split into different levels and each level is placed according to a hierarchy. These levels have direct or indirect relationship with one another. The various levels in a standard organization are as follows −
- Company
- Company code
- Plant
- Storage location
- Purchasing organization
- Purchasing group
All the Definitions in SAP are given through the Display IMG screen as shown below −
Path to reach Definition
IMG ⇒ Enterprise Structure ⇒ Definition

Create Company
Company is the topmost organizational unit after client, which incorporates individual financial accounting statements of several company codes. A company can have many company codes. In SAP, it is optional to create a company. The following steps will take you through the procedure of creating company.
Path to Create Company
IMG ⇒ Enterprise Structure ⇒ Definition ⇒ Financial Accounting ⇒ Define Company
TCode: OX15
Step 1 − On the Display IMG screen, select Define Company execute icon by following the above path.

Step 2 − Click the New Entries icon.
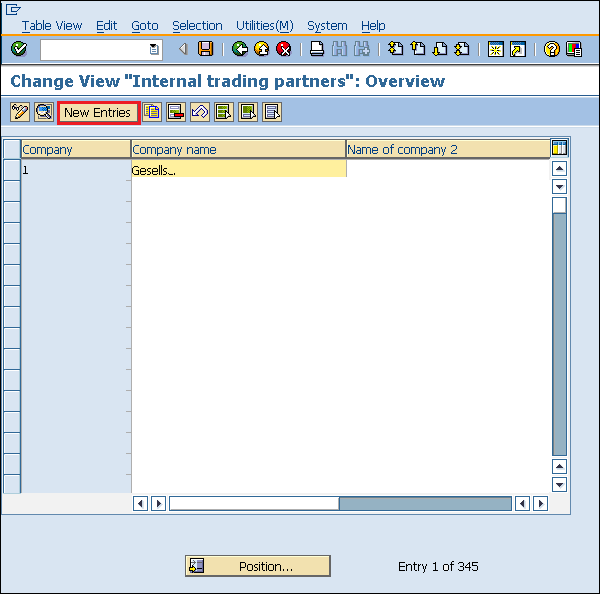
Step 3 − Fill in all the necessary details such as name of the company, address of the company with street number, city, country, and postal code.

Step 4 − Click the Save icon after filling the required information. A new company will be created.
Create Company Code
A Company Code is the smallest organizational unit after company, for which the standalone financial accounting's profit and loss statements can be withdrawn. Many company codes can be assigned to one company. The following steps depict how to create a company code.
Path to create Company Code
IMG ⇒ Enterprise Structure ⇒ Definition ⇒ Financial Accounting ⇒ Edit, Copy, Delete, Check Company Code
TCode: OX02
Step 1 − On the Display IMG screen, select Edit, Copy, Delete, Check Company Code execute icon, by following the above path.

Step 2 − Click the New Entries button.

Step 3 − Fill in all the necessary details like Company code, company name along with city, country, currency, language.

Step 4 − Click the Save icon after filling the required information. A new company code will be created.
Create Plant
A Plant is an organizational unit within a company where activities take place. A plant will produce goods and make goods available for the company. The following steps will take you through the procedure of creating a plant −
Path to create Plant
IMG ⇒ Enterprise Structure ⇒ Definition ⇒ Logistic General ⇒ Define, Copy, Delete check plant
TCode: OX10
Step 1 − On the Display IMG screen, select Define, Copy, Delete check plant execute icon, by following the above path.
Select Define Plant icon to create a new plant.

Step 2 − Click the New Entries icon.

Step 3 − Fill in all necessary details like plant name along with detailed information like Language, House no., city, country, region, postal code.

Step 4 − Click the Save icon after filling the required information. A new plant will be created.
Create Storage Location
A Storage Location is an organizational unit, which actually differentiates between the different material stocks in a Plant. Storage location is a place where stock is kept physically. A plant can consist of multiple storage locations. All data is stored at a storage location level for a particular storage location. Follow the steps given below to create a Storage Location −
Path to Create Storage Location
IMG ⇒ Enterprise Structure ⇒ Definition ⇒ Materials Management ⇒ Maintain Storage Location
TCode: OX09
Step 1 − On the Display IMG screen, select Maintain Storage Location execute icon, by following the above path.

Step 2 − Enter the name of the plant for which you want to create the storage location.

Step 3 − Click the New Entries icon.

Step 4 − Enter the name of the storage location along with its description. Click the Save icon after filling the required information. A new Storage Location will be created.
Create Purchasing Organization
A Purchasing Organization is an organizational unit under Company or Plant that is responsible for procurement activities according to requirements. It is responsible for external procurement. A purchasing organization can be specific to a plant or a company. Following the steps given below to create a Purchasing Organization −
Path to Create Purchasing Organization
IMG ⇒ Enterprise Structure ⇒ Definition ⇒ Materials Management ⇒ Maintain Purchasing Organization
TCode: OX08
Step 1 − On the Display IMG screen, select Maintain Purchasing Organization execute icon, by following the above path.

Step 2 − Click the New Entries icon.

Step 3 − Enter the name of the purchasing organization along with its description.

Step 4 − Click the Save icon after filling the required information. A new Purchasing Organization will be created.
Create Purchasing Group
A Purchasing Group is an organizational unit that is responsible for the everyday procurement activities within an organization. The steps given below depict how to create a Purchasing Group −
Path to Create Purchasing Group
IMG ⇒ Materials Management ⇒ Purchasing ⇒ Create Purchasing Group
TCode: OME4
Step 1 − On the Display IMG screen, select Maintain Purchasing Group execute icon, by following the above path.

Step 2 − Click the New Entries icon.

Step 3 − Enter the name of the purchasing group along with its description.

Step 4 − Click the Save icon after filling the required information. A new Purchasing Group will be created.
Regards
SAP-MM4U